XRH Count Inline
Fully automated component counting
Software Specification
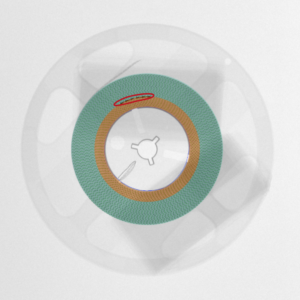
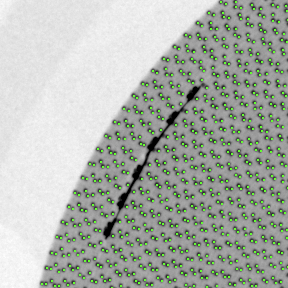
Splicing Detection
Metal splicing is common and widely used on SMD electronic industry, connecting two tapes. During X-ray counting process the image acquired shown the splicing visible as a dark spot.
The artificial intelligence of the XRHCount has a special algorithm to detect the metal splicing. When it is localized it gets excluded from the counting algorithm.
Excluding this identified, dark spot the result more reliable, since its poorly possible to determine if the metal pocket is empty or not. Assuming its not empty brings risks to your material inventory control.
The computationally intensive applications optimise the counting results with an exclusive technique. Direct post-processing of the images creates the highest possible counting accuracy, which distinguishes the XRHCount.
The user can track the data of the reel.
- Number of splices on the reel
- Number of components before and after the splice
- Exclude the area of the splicing from the counting algorithm
- The amount of each area can be submitted to the ERP system
- The partial quantities can be printed on the new label
The splicing detection combined with the ASM Material Managers enables the functionality to update each unique ID between the splicings.
Statistic Suite
The Statistic- & Maintenance Suite fosters what has been called a "smart factory".
The predictive information on the maintenance tab is a based solution for management problems of the system. It is an example of how big data analytics and advanced AI algorithms can help detect part failures via hidden correlations that otherwise would be impossible to find, hereby avoid failures before they happen.
The Statistic- & Maintenance Suite is supporting the local maintenance team for serving the management in an optimal way.
The maintenance area is displaying the condition of the system. To perform a preventive maintenance visit at the right time, the engineers can track different data. The key values are: X-ray tube hours, light barrier faults, emergencies, drawer cycles, start button pressed and software updates.
The Statics tab helps and displays easily the system utilization, the frequency can be sorted out per day, week, month or year of the system.
With this data, the ROI can easily calculate and the management can track system performance either operational performance.
System communicates and cooperates with real-time data that can be shared across organizational dashboard offering a competitive advantage in supply value chain!
The XRHCount Inline software is self-explanatory. Operation is particularly easy thanks to the intuitive programme and the user-friendly Graphical User Interface (GUI). This eliminates the need for expensive training for setting up and integrating the system into production.
The standard interface of the XRHCount Inline is the Hermes protocol (The Hermes Standard). It thus brings Industry 4.0 to SMT electronics production. All stations of the production line are connected to each other thanks to the protocol and exchange information. This enables seamless traceability of the parts without loss of data. And this over the entire production cycle.
Of course, the SMEMA standard can also be used if required. Just as the customer wishes and as it fits into the existing production.